What are Specialty Lubricants?
Specialty lubricants are engineered oils, greases, and pastes designed to meet the specific needs of specialized equipment and demanding environments. Unlike general-purpose lubricants, which primarily aim to reduce friction and wear in relatively standard conditions, specialty lubricants are tailored to perform under unique and challenging conditions. This can include extreme temperatures, high-pressure loads, chemical exposure, or even environments where contamination is a significant concern.
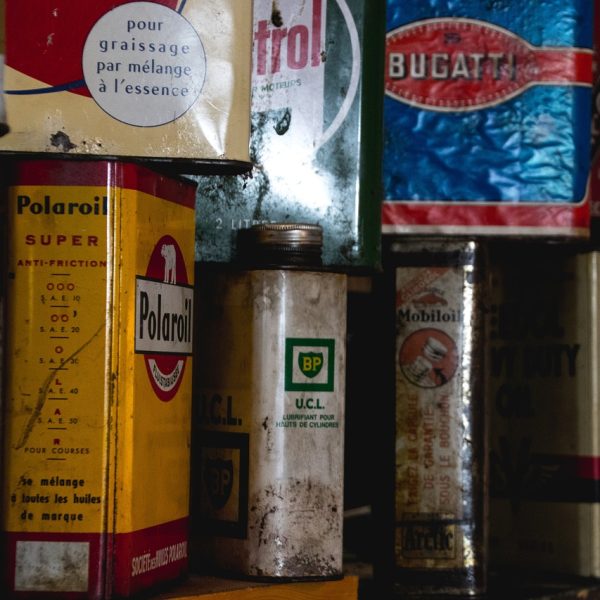