Introduction to Solid Lubricants
Lubrication is essential in mechanical engineering, where components frequently move against each other, causing friction, wear, and energy loss. Traditional liquid lubricants, such as oils, are widely used for these purposes. However, when machinery operates in extreme temperatures, high-vacuum environments, or conditions that might cause liquid lubricants to evaporate or degrade, solid lubricants offer a robust alternative.
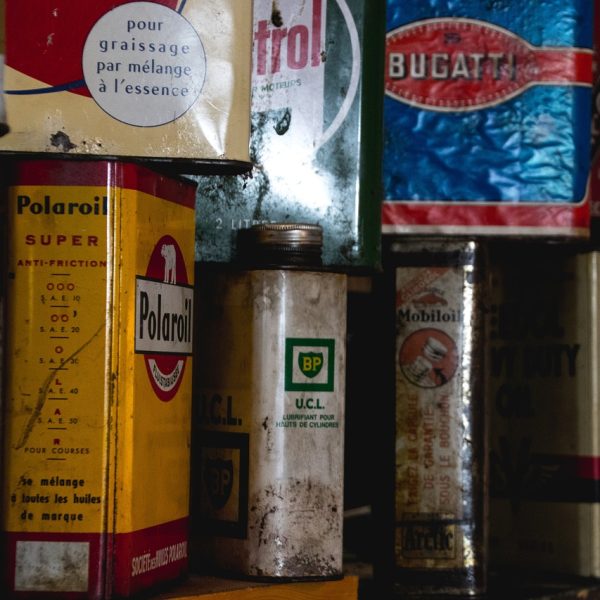